Nylon Reinforcements in Composites: Boosting Structural Integrity
- Faisal
- Nov 4, 2024
- 4 min read
In the world of advanced materials, the use of composites has revolutionized various industries, from automotive and aerospace to construction and consumer goods.
One of the critical components in the development of high-performance composites is the incorporation of nylon reinforcements.
Nylon, a versatile and robust polymer, enhances the structural integrity of composites, offering numerous benefits that make it a preferred choice for engineers and manufacturers. In this blog, we will explore the role of nylon reinforcements in composites, their advantages, and the wide range of applications they serve.
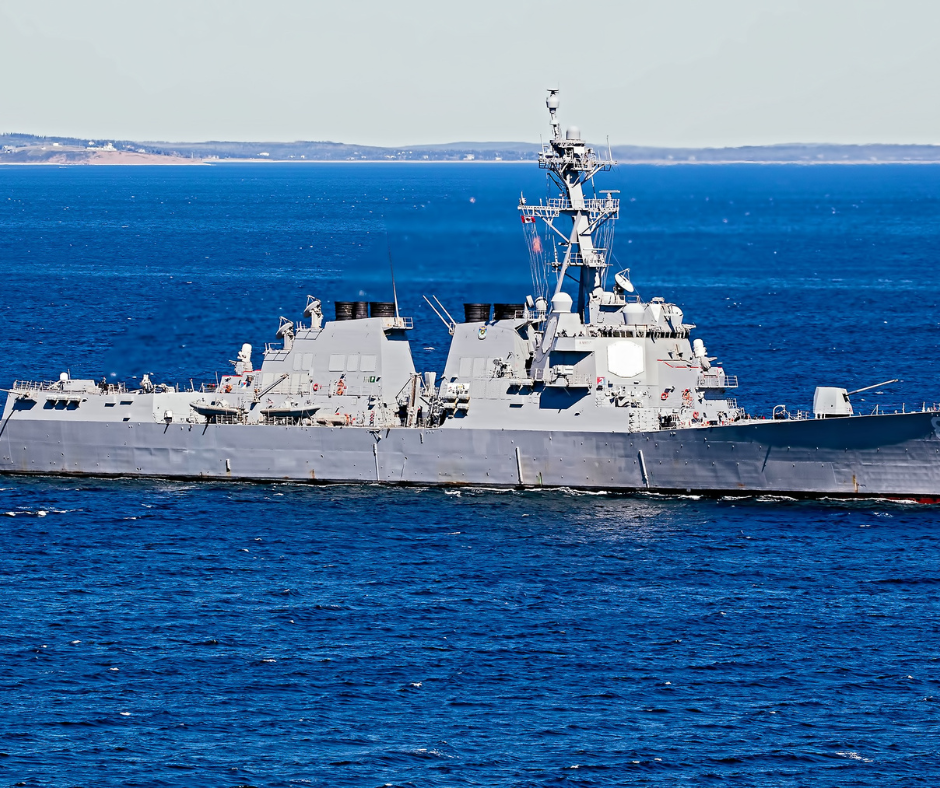
Understanding Nylon Reinforcements
Nylon, also known as polyamide, is a synthetic polymer known for its excellent mechanical properties, chemical resistance, and durability. When used as a reinforcement material in composites, nylon fibers or fabrics are embedded in a matrix, such as epoxy or polyester resin, to create a material that combines the strengths of both components. This synergy results in composites that are stronger, lighter, and more resilient than their individual constituents.
Key Properties of Nylon Reinforcements
High Tensile Strength: Nylon fibers possess high tensile strength, which contributes to the overall load-bearing capacity of the composite material.
Impact Resistance: Nylon-reinforced composites exhibit excellent impact resistance, making them suitable for applications that require durability and toughness.
Flexibility and Elasticity: Nylon fibers provide flexibility and elasticity, allowing the composite to absorb and dissipate energy, reducing the likelihood of fractures and damage.
Chemical Resistance: Nylon is resistant to a wide range of chemicals, including oils, solvents, and fuels, ensuring the longevity and performance of the composite in harsh environments.
Thermal Stability: Nylon maintains its properties over a broad temperature range, making it ideal for applications exposed to varying thermal conditions.
Low Moisture Absorption: Nylon fibers have low moisture absorption, preventing swelling and maintaining the dimensional stability of the composite.
Advantages of Nylon Reinforcements in Composites
1. Enhanced Structural Integrity
Nylon reinforcements significantly enhance the structural integrity of composites by providing high tensile strength and impact resistance. This makes the composite material robust and capable of withstanding substantial mechanical stresses, which is crucial for applications in demanding environments.
2. Weight Reduction
One of the primary benefits of using composites is weight reduction. Nylon-reinforced composites are lighter than traditional materials like metals, which translates to improved efficiency and performance in applications such as automotive and aerospace. The reduction in weight also contributes to energy savings and lower operational costs.
3. Design Flexibility
The versatility of nylon fibers allows for greater design flexibility in composite manufacturing. Engineers can tailor the properties of the composite by adjusting the orientation, density, and type of nylon reinforcement used. This customization enables the creation of materials that meet specific performance criteria for diverse applications.
4. Durability and Longevity
Nylon's resistance to chemicals, moisture, and thermal variations ensures the durability and longevity of the composite material. This durability reduces the need for frequent maintenance and replacements, resulting in cost savings over the lifecycle of the product.
5. Improved Safety
In applications where safety is paramount, such as automotive and aerospace, nylon-reinforced composites offer superior impact resistance and energy absorption. This enhances the safety of structures and components, protecting both users and equipment.
Applications of Nylon-Reinforced Composites
1. Automotive Industry
In the automotive industry, the demand for lightweight, durable materials is ever-growing. Nylon-reinforced composites are used in the manufacture of various components, including body panels, bumper systems, and structural parts. The material's high strength-to-weight ratio and impact resistance contribute to improved fuel efficiency and enhanced safety in vehicles.
2. Aerospace Industry
The aerospace industry benefits greatly from the use of nylon-reinforced composites due to their lightweight and robust nature. Components such as interior panels, seat frames, and structural elements are often made from these composites, helping to reduce the overall weight of the aircraft and improve fuel efficiency.
3. Construction Industry
In construction, nylon-reinforced composites are used for applications that require high durability and resistance to environmental factors. Examples include reinforcement bars (rebar), structural panels, and bridge components. These materials provide enhanced structural integrity, longevity, and resistance to corrosion compared to traditional materials like steel and concrete.
4. Consumer Goods
Nylon-reinforced composites are also prevalent in the consumer goods sector. They are used to manufacture durable and lightweight products such as sporting goods, luggage, and electronic housings. The material's versatility and performance characteristics make it ideal for producing high-quality consumer products.
5. Industrial Applications
In industrial settings, nylon-reinforced composites are utilized for manufacturing equipment and components that require high strength and resistance to wear and tear. Applications include conveyor belts, gears, and bearings, where the material's durability and low friction properties are advantageous.
6. Marine Industry
The marine industry leverages the benefits of nylon-reinforced composites for applications such as boat hulls, decking, and structural components. The material's resistance to moisture and saltwater, combined with its high strength, makes it ideal for the demanding marine environment.
Innovations and Future Trends
The field of nylon-reinforced composites is continually evolving, with ongoing research and development aimed at enhancing the properties and expanding the applications of these materials. Innovations such as hybrid composites, which combine nylon with other reinforcing materials like carbon fiber or glass fiber, are being explored to achieve even greater performance characteristics.
Additionally, advancements in manufacturing techniques, such as 3D printing and automated fiber placement, are enabling more efficient and cost-effective production of nylon-reinforced composites. These technologies offer new possibilities for complex and customized designs, further broadening the scope of applications.
Sustainability is also a growing focus in the development of nylon-reinforced composites. Efforts are being made to utilize recycled nylon fibers and bio-based resins, reducing the environmental impact of composite production and contributing to a circular economy.
Conclusion
Nylon reinforcements in composites play a crucial role in boosting the structural integrity of materials used across various industries. Their unique combination of high strength, impact resistance, flexibility, and chemical resistance makes them an ideal choice for applications that demand durability and performance. From automotive and aerospace to construction and consumer goods, nylon-reinforced composites are paving the way for innovative and sustainable solutions.
As the demand for advanced materials continues to grow, ongoing research and technological advancements will further enhance the properties and applications of nylon-reinforced composites. By leveraging the benefits of these materials, manufacturers can develop high-performance products that meet the challenges of modern engineering and contribute to a more sustainable future.
For more information on nylon reinforcements in composites and their applications, contact leading suppliers and manufacturers of advanced materials. Discover how nylon-reinforced composites can enhance the performance and sustainability of your products, driving success in your industry.
A Funded Account Forex opportunity is available at Winprofx for skilled traders aiming to scale their performance. Trade with real capital, showcase your strategy, and earn profit splits without risking your own money. This model rewards discipline, consistency, and smart risk management. Gain access to a professional environment that supports growth and performance tracking. With clear objectives and structured evaluation, traders can prove their expertise and get rewarded accordingly. Enjoy a new level of freedom and potential with a funded account designed for serious market participants.
La Jugabet app facilita apostar desde el móvil con rapidez y seguridad. Su diseño intuitivo permite acceder a deportes y esports fácilmente, además de aprovechar promociones exclusivas. Ideal para quienes quieren apostar en cualquier lugar sin complicaciones.
Phantom Wallet Extension and Cash App Login offer secure, user-friendly access to digital finance tools. Phantom enables seamless Solana token and NFT management, while Cash App Login provides easy entry to money transfers, Bitcoin trading, and stock investments. Together, they empower users with fast, secure, and convenient crypto and finance experiences. Phantom Wallet Extension | Cash App Login
Just wanna give a 🚀quick shoutout to " No1AssignmentHelp .Com" – 🔊honestly, they're a lifesaver! It was flat out with uni work and needed a hand, and these legends came through big time⏲. If you're after the 🔍 Best Assignment Help around, you can't go wrong here. The work's spot on, delivered✍ quickly, and helped me boost my grades 🥇without the stress😀. Bloody brilliant service – cheers, team!
More Links to Visit
👉 Assignment Help Australia ➡➡➡➡➡➡➡➡➡➡➡➡➡➡➡➡➡➡➡➡➡➡👌👍✅🆗
👉 MBA Assignment Help ➡➡➡➡➡➡➡➡➡➡➡➡➡➡➡➡➡➡➡➡➡➡➡➡👌👍✅🆗
👉 Nursing Assignment Help ➡➡➡➡➡➡➡➡➡➡➡➡➡➡➡➡➡➡➡➡➡➡👌👍✅🆗
👉 Law Assignment Help ➡➡➡➡➡➡➡➡➡➡➡➡➡➡➡➡➡➡➡➡➡➡➡➡👌👍✅🆗
👉 Finance Assignment Help ➡➡➡➡➡➡➡➡➡➡➡➡➡➡➡➡➡➡➡➡➡➡👌👍✅🆗
👉 Marketing Assignment Help ➡➡➡➡➡➡➡➡➡➡➡➡➡➡➡➡➡➡➡➡➡👌👍✅🆗
👉 Economics Assignment Help ➡➡➡➡➡➡➡➡➡➡➡➡➡➡➡➡➡➡➡➡👌👍✅🆗
👉 Computer Engineering Assignment Help ➡➡➡➡➡➡➡➡➡➡➡➡➡➡👌👍✅🆗
👉 Dissertation Help ➡➡➡➡➡➡➡➡➡➡➡➡➡➡➡➡➡➡➡➡➡➡➡➡➡➡👌👍✅🆗
👉 Research Paper…
The Rise of Nylon in Malaysia’s Composite Industry
Malaysia’s industrial landscape is rapidly evolving, with nylon-based composites becoming a vital material in automotive and aerospace manufacturing. Known for their durability, flexibility, and resistance to wear, these composites are revolutionizing engineering practices across the country. As industries grow, so does the need for well-researched academic support in this niche field.
Students pursuing engineering and material sciences often find themselves grappling with complex topics like polymer science and composite behavior. To bridge this gap, many turn to reliable Academic Writing Services in Malaysia. These services provide expert guidance and high-quality content, helping students excel in technical assignments and research papers related to advanced materials like nylon composites.
With the academic and industrial worlds…